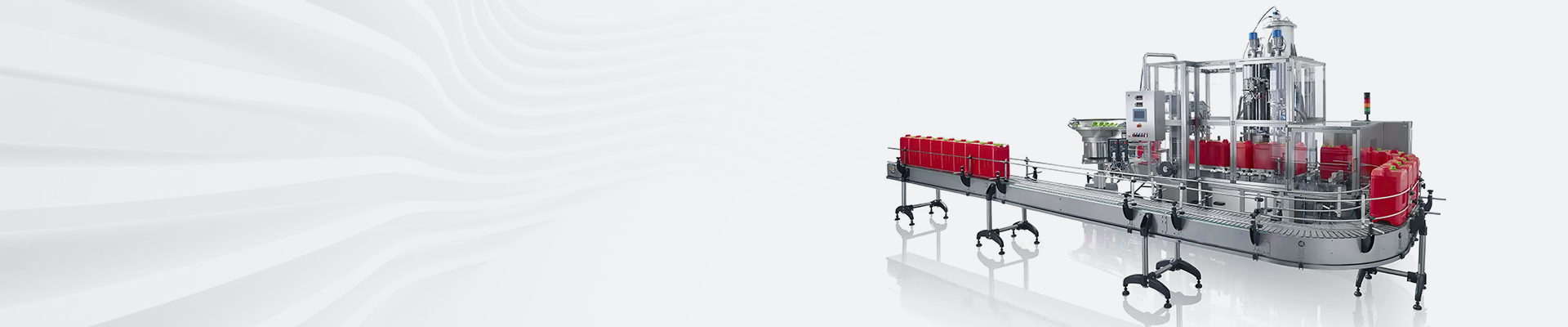
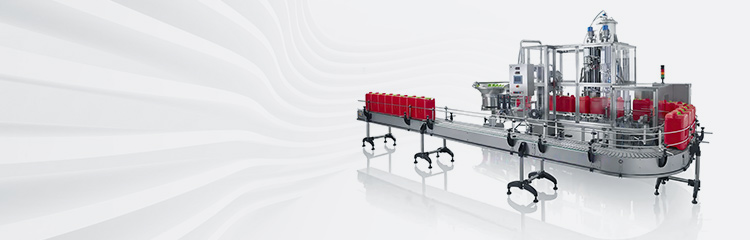

Summary:The batching system uses S7200 PLC as the measurement and control core, td400c as the human-machine interface unit, FS11 series frequency converter to control the motor speed, the pressure weighing module as the weighing component, and the speed measurement module as the speed measurement component. Online dynamic weighing solves the problem of instability. error, improving the accuracy of batching.
The feeding system needs to design PLC control in the following aspects:
1) The overhead crane PLC interacts with the unit, accepts the data sent down from the unit and feeds back the data to the unit.
Crane automatic feeding trigger condition is to be able to obtain data sent, data sent under the premise of communication, the need to meet the host computer or other control machine and crane PLC normal communication, in order to ensure the normal interaction of data.
2) Crane PLC control of large and small cars and lifting frequency converter to complete the crane transit.
One of the logic of the overhead crane PLC is to control the big, small car and lifting frequency converter automatic and safe operation, the core of controlling the operation of the crane is to control the operation of the frequency converter, under the premise of ensuring that the hardware connection is error-free, can be realized through the corresponding logic control.
3) Crane PLC logic control disk suction and discharge. One of the logic of the overhead crane PLC is to control the disk when to suck the material, when to put the material.
4) overhead crane PLC and transfer car normal communication for the corresponding body number of data transfer car on the charging trolley for transfer to the furnace before charging, and in the charging trolley to leave the charging position, the overhead crane PLC needs to pause charging until the charging trolley to reach the charging position can continue to add material. This process requires the overhead crane system and transfer vehicle system for communication and data interaction, so to ensure normal communication between the two is one of the needs of the design.
5) The PLC of the overhead crane communicates with the hook scale to obtain the corresponding weight data. Feeding process, real-time weight data acquisition is the premise of the feeding system error and normal operation, through stable wired communication is to ensure that the weight of the basis for obtaining.
2 system design
2.1 State machine of dosing control system
The PLC of the overhead crane, under the premise of maintaining normal communication with the intelligent unit, acquires the data issued by the unit, and starts to run under the conditions of automatic operation, and the disk starts to rise, and rises to the safe operation position; the big car and the small car start to run, and run to the top of the corresponding material pit, and the big and small cars can run at the same time; the disk descends, and touches the bottom of the material pit, and then the disk powers up to absorb the material after judging the position of transferring car in the dosing position; the disk rises to the dosing position, and judges whether it is a dosing position or not. Rise to the dosage position, determine whether the need for dosage, if the need for dosage into the dosage state machine, if the need for dosage is not required then the disk rises to the operating height; the size of the car running to the discharging position; disk down to the discharging position of the discharge of the material; at this time the PLC to determine whether it has been dosed to complete, if completed, then return to the leisure area to wait for the next time the data is sent out, if it is not completed, the cycle continues to unfold from the second step.
The implementation of the entire control system will be improved and supplemented under this framework, the overall control state machine is the basis for the realization of the automatic feeding of the overhead crane.
2.2 Equipment chain
The overhead crane PLC in this feeding system needs to complete communication with three devices, namely the intelligent unit, the hook scale receiver and the transfer vehicle. With the hook scale through the RS232 serial communication mode, with the intelligent unit through the ModBusTCP/PEthemmet communication mode, with the transfer vehicle through the ModBusTCP communication mode to complete the communication.
1) KepWare in the intelligent unit through the establishment of ModBusTCP/IPEthemmet channel, under the channel according to the specific LAN IP address of the overhead crane PLC to connect, and complete the data reading and writing; overhead crane system and the intelligent unit communication data include: complete, send weight data, the system operating status, furnace number sent, charging start signal, the system alarm state etc.
2) The transfer trolley is controlled by Schneider PLC. Transfer car PLC and overhead crane PLC between the two to achieve a kind of interlocking function, that is, when the crane system in the disk down to the suction position to determine that the charging trolley has left the charging position, it is necessary to pause the charging until the charging trolley in place to receive the signal, before continuing to charge; when the transfer car system to determine the overhead crane system disk has been powered up to prohibit charging trolleys from leaving the charging position, wait for the completion of the discharge of the disk and the charging trolley, before the charging trolley transfer. When the transfer vehicle system judges that the disk of the overhead crane system has been powered up to prohibit the feeding trolley from leaving the feeding position, it waits for the disk to finish discharging and leave the feeding trolley before the feeding trolley is transferred. So the two Schneider PLC can communicate with each other through ModBusTCP, add the corresponding communication program segment in the PLC programming, and define the packet traffic between the two. The variables of the overhead crane system and the transfer car system mainly include: the heartbeat of the overhead crane system and the transfer car system, the feeding trolley is in place, the feeding trolley leaves, and prohibits the feeding trolley from leaving the signals 2.3, the dosage state machine
Disk suction and discharge weight and voltage correspondence is not a relative linear relationship, but an irregular dosage curve, which needs to be tested to get a certain amount of data curve fitting, so as to better realize the dosage function. For each material, the dosage curve obtained through testing is also different. Dosing state machine process as shown in Figure 4, after the disk suction to the dosing position, to determine whether the weight of the material is now more than the remaining weight of the range, if out of range, then start the implementation of the dosing state machine, according to the different materials have been measured by the dosage curve to give a certain voltage, to complete the first mixing; if the error still does not reach the range, it is necessary to gradually reduce the voltage, each time to reduce the voltage until the weight error is allowed. Reduce the voltage until the weight error is within the allowable range.
2.4 Encoder value acquisition and calibration
The encoder, as the measurement unit for judging the traveling position in this system, plays a vital role. The hardware connects the encoder to the PLC, and the high-speed counter in the PLC takes the value and calculates through the data, so as to determine the traveling position.
Through the two input points access, set up the A, B phase in the equipment level, define the counting method as normal integration mode, so that the value of high-speed counter can be obtained.
This system uses incremental encoder, and high-speed operation, the encoder is bound to error, which requires the process of setting up some checkpoints, when the car running to the checkpoint, the preset value written into the encoder as a check!
2.5 Data analysis and alarm
Data analysis includes: encoder value judgment position, material pit position judgment, five-point suction method cycle, the size of the car running state judgment, suction state judgment, the remaining weight and the weight has been added to the record, the program cycle reset, transfer car system data analysis.
Alarm signals include: carriage position compliance detection, hook scale tare alarm, dosage failure alarm, weighing weight loss alarm, encoder data error alarm, and transfer truck communication alarm.
Five-point suction method:The radius of the disk is small relative to the entire pit. There is a problem that it is not possible to suck the whole material of the pit at the same position of the pit. A point can not solve the problem requires more points spread out, through a number of points of rotation, in order to ensure that the entire pit of materials can be absorbed. The basic principle is shown in Figure 5, the first polling for the first point, the second polling for the second point, and so on.
Encoder position judgment: in the process of running the car, the role of the encoder is very important, the car whether to reach the destination, whether to enter the deceleration zone, whether in the danger zone and so on need to judge the value of the encoder to make the corresponding action.
Dosage failure alarm: the dosage step mentioned above, can not do every time to be able to successfully dosage, when the real-time value of the dosage is less than the minimum value of the system calculations given the acceptability of the dosage fails to put the material and repeat the dosage suction dosage step. When the dosage failure occurs three times, the system decides to give up the dosage, and informs the workers in the form of alarm that the dosage fails in this tray until it is reset manually or automatically.
Encoder alarm: system PLC appears long time power failure, inverter failure, connection is not normal, etc. Incremental encoder will often appear in the phenomenon of numerical disorder, if such a situation, once the automatic dosing began to run, the traveling car will appear "out of control" phenomenon, can not reach the designated position to make the specified action, is a very dangerous thing! This is a very dangerous thing. Therefore, it is especially important to determine the compliance of the encoder data. If the encoder value alarm occurs, it can only be reset manually after ensuring that the value is calibrated.
Loss of weight alarm: weight data is an important parameter for dosage, any error, inaccuracy or loss of data will make the calculation of dosage data wrong, adding unnecessary trouble of dosage mixing for pre-furnace dosage. Therefore, the system to determine the loss of weight data to alarm notification, to be identified and resolved before continuing to use the automatic dosage.
Communication alarm with transfer car: abnormal communication with transfer car leads to data loss, which means that the automatic dosing system can not get the correct position information of the dosing trolley. For example: the feeding trolley has left the feeding position, but due to the communication abnormality, the system gets the signal of the last feeding trolley in the feeding position, which leads to all the added materials spilling outside. 2.6 Realization of anti-swing function
In order to maintain the stability of the trolley in operation and reduce the error caused by the swing and shake, it is necessary to do certain motion control on the trolley so that it can minimize the swing in operation. Schneider Electric in the anti-swing aspects of the PLC and frequency conversion to do some of the necessary settings to meet the user's needs in this area.
3.1 Realization of operation function
Calculate the target position and the actual position of the deviation, the positive value for the forward, and vice versa, the negative value for the backward, and get the absolute value; determine whether the distance difference for the allowable error range, if in the allowable error range, to stop the run; determine the real-time weight value of the disk, if the weight value is less than the negative value of the empty weight of the disk, then the disk is in the landing state; the size of the car and the lifting operation requires a series of judgment conditions that is, the logic of the bit, such as the lifting Running limit conditions are: big car stationary state, small car stationary state, traveling car running state, automatic running state, lifting limit open state. 3.2 Alarm state realization
Car position compliance detection: large and small cars and lifting any position of the encoder is not within the safety range, the state is set to 1; dosage failure alarm: three consecutive dosage steps in the dosage step have failed, the state is set to 1, until the next dosage step or cut back to the manual from the automatic reset; weight loss alarm: set a timer, the state of ten seconds did not receive the state of the receiver data of the hook scale, the state is set to 1; with the transfer vehicle communication alarm: the state of the transfer vehicle communication is set to 1, the state is set to 1. Transfer vehicle communication alarm: the traveling system and the transfer vehicle system ensure communication by sending each other heartbeats, set the timer, if no heartbeat signal is received from the transfer vehicle within five seconds, the status will be set to 1.
3.3 The realization of data analysis function
Judgment of suction state: two states of suction and discharge under manual state and two states of suction and discharge under automatic state; Finished weight record: record and add up for each kind of material each time when discharging is finished, until restarting the charging system; Calculation of residual weight, the total weight minus the added weight to get the residual weight after obtaining the weight that has been added; Calculation of tolerance: each time when charging can't be done without any difference, it is necessary to calculate the permissible tolerance according to the total weight of material that has been added. The total weight of the material is calculated based on the total weight of the allowed error range, such as when the total weight <2t, the tolerance is 50kg, when the total weight >2t, the tolerance is calculated as 5% of the total weight; charging car weight upper limit settings: charging car space and bear weight is limited, need to set the upper limit to determine whether to pause the process of charging and wait for the next empty car in the charging position; charging cycle: the order of the material is specified in advance, and in the charging cycle Judge whether to carry out the next material feeding process.
3.4 The realization of anti-swing function
Use the existing anti-sway function block to process the data simply, mainly for the acceleration and deceleration process of the acceleration control.
4 Conclusion
Casting melting furnace automatic charging system through the transformation of software and hardware, hardware replacement for the ability to receive PLC control equipment, mainly using PLC programming to achieve the casting melting part of the furnace after the automatic charging. Can meet the needs of the vast majority of factories at present after the furnace automatic charging. Achieve the purpose of reducing manual labor, unmanned, and increase the efficiency of the furnace charging for the foundry industry melting plant to reduce the cost of manpower and time.
The design of the automatic post-furnace feeding system has achieved the results of multi-point suction, but there are still some shortcomings to be further improved.
1) Due to the uneven distribution of materials in the pit, there may be empty suction phenomenon, in the future, with the enhancement of artificial intelligence recognition technology, increase the identification of materials in the pit, to achieve automatic judgment of the location of the material and suction.
2) The degree of realization of the anti-sway function is not the same, and the number of lifting wire rope and walking distance to meet the conditions of stable operation of the vehicle and other factors are directly related to the future need to achieve further breakthroughs in the anti-sway function of the vehicle.