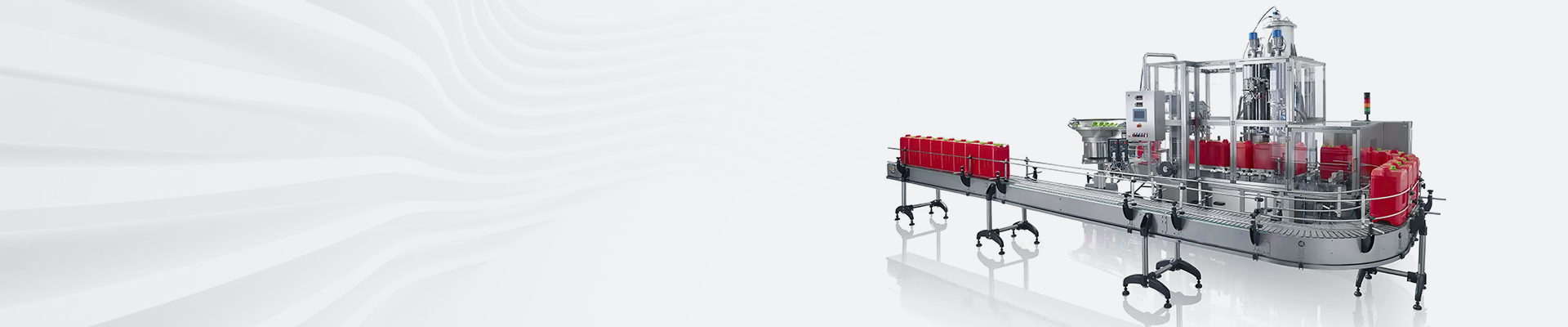
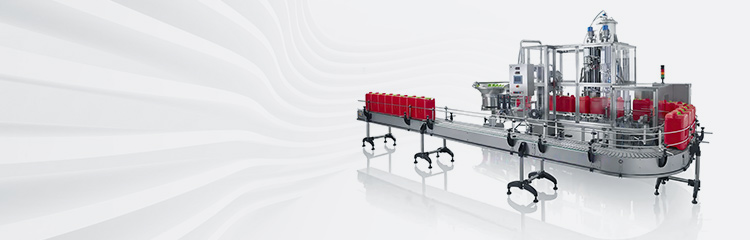

Summary:The touch screen is used as the backup controller of computer control, when the computer system can not work normally, the touch screen assumes the management of the dosage system and various dosage parameter modification functions, so that the system can continue to normal dosage, thus further improving the reliability of the system. Touch screen communicates with PLC through MPI protocol.
1 Preface
At present, most of the rubber factories in China use the dosage control system developed in the 1980s, which mainly consists of computers, dosage controllers, PLCs, feeding control devices, etc. The dosage controller controls the replenishment and discharge of each scale, and the PLC controls the dosage timing. The dosage controller controls the replenishment and discharge of each scale, PLC controls the dosage timing, and the computer monitors and manages the whole dosage process. There is a large amount of data exchange between the dosage controller, PLC and computer of this system.
2 the main shortcomings of the traditional dosage control system
2.1 System hardware line complexity
In traditional dosage control system, there are a lot of 1/0 interfaces between dosage controller and PLC, dosage controller and feeding control device, PLC and feeding control device, and there are communication network lines between dosage controller and computer of each scale. Such a system structure determines the complexity of its hardware lines. 2.2 Poor reliability of the communication between the computer and the dosage controller due to the computer does not have a special software to communicate with the dosage controller, the communication software between the computer and the dosage controller is used by each dosage system supplier with "VB" or "VC". VB" or "VC" and other language programming for communication, it is inevitable that the consideration is not good, the control process will appear communication is not smooth, real-time use of incorrect data and other issues.
2.3 System reliability is not high
Because the rubber dosage is a long-term continuous work, the complexity of the system hardware line and the poor communication reliability of the computer and the dosage controller determines its system reliability is not high, troubleshooting is difficult, maintenance is not convenient.
3 new dosage control system composition
3.1 The structure and principle of the new dosage control system
With the rapid development of electronic technology, PLC is more and more powerful, more and more used in a variety of control areas. PLC has developed from the traditional sequence control to control a variety of industrial needs, which is specifically applied to the dosage of the dosage control module to achieve dosage control. The computer control software supporting PLC is also more and more, the world's major computer control software can support the mainstream PLC, so that the data exchange between computer and PLC becomes simple and reliable. Siemens PLC is one of the world's best PLC, its SIWAREX weighing module is applied to S7-300, S7-400PLC dosage module. The new dosage control system is to replace the dosage controller with PLC weighing module, so that the whole dosage process is carried out under the control of PLC. The new dosage control system consists of computer, PLC, feeding control device and so on.
The sensor signal of each scale directly enters into the corresponding weighing module, and the computer PLC communicates with each other through PROFIBUS communication protocol, and the PLC directly controls the replenishment and discharging of each kind of material of each scale according to the dosage time sequence.
The touch screen is used as a backup controller for computer control. When the computer system can not work normally, the touch screen assumes the management of the dosage system and various dosage parameter modification functions, so that the system can continue normal dosage, thus further improving the reliability of the system. The touch screen communicates with PLC through MPI protocol.
3.2 Hardware equipment of new type batching control system
The computer system adopts high-quality industrial control machine or server to ensure the reliability of the computer system. PLC adopts Siemens S7-300, S7-400 PLC. from the function of S7-300, S7-400 can realize the control, considering S7-400 is much more expensive than S7-300, from the point of view of the consideration of the system cost, generally S7-300 is used. when the CPU to be a few remaining, S7-400 and E7-400 are used. The combination of S7-400 and ET200 is used. Touch screen with Siemens S7 series PLC communication products, such as DIGITAL or GE and other companies. Electromagnetic vibration feeder is controlled by electromagnetic vibration feeder control device, and screw feeder is controlled by frequency converter.
3.3 Software of new type batching control system
The computer software adopts the standard computer monitoring software which supports PROFIBUS protocol to ensure the smooth and reliable communication between computer and PLC. Computer monitoring software can be used in the United States GE's CIMPLICITY or Siemens WinCC and so on. In addition to the main screen of dosage control, the computerized monitoring software also has the control screens of weighing point management, dosage parameter management, recipe management, dosage time sequence management, parameter calibration, report management and fault alarm, etc. The operation is intuitive and simple. Computerized report management adopts SOLServer and Excel, which ensures that the batching data cannot be changed and facilitates statistical management.
PLC software is programmed by Siemens STEP7, PLC control software includes weighing module data conversion, scale replenishment and discharge control, dosage timing control, mixing timing control, and various fault detection alarms.
The touch screen software is programmed by its special software. The touch screen has the necessary operation interface and corresponding control functions for the dosage process.
Siemens provides special calibration software SIWATOOL for SIWAREX weighing module, the computer and SIWAREX weighing module adopt RS232 communication, and the calibration is realized through the SIWATOOL software on the computer, the SIWATOOL calibration software makes the original complex calibration process become simple and intuitive.
4 new dosage control system features
4.1 System reliability
High system hardware configuration advanced, computer and PLC communication smooth, determines the high reliability of the system.
4.2 High dosage accuracy
Due to the high measuring accuracy of weighing module, at the same time, PLC program can be programmed according to the special requirements of the scale, which makes it have high dosage accuracy. The static accuracy of the system is 1/1500 (the static accuracy of 10kg~100kg small scale is 1/800) and the dynamic accuracy of the system is 1/800 (the dynamic accuracy of 10kg~100kg small scale is 1/400). The weighing accuracy of the special small scale can reach 2g, which can meet the special requirements of rubber factories for all kinds of dosage including special rubber.
4.3 Easy system maintenance
Simple hardware line, few intermediate links, good hardware quality, so that the system is almost maintenance-free. The system has various automatic diagnostic functions for faults, and the fault points are clear at a glance, so it is convenient to remove the faults quickly. The plug-in and plug-out input and output terminals of Siemens PLC can easily replace the PLC module.
4.4 Realize discharge speed control
According to the process requirements, it automatically outputs 4mA~20mA control signals to regulate the speed of the discharge feeder.
4.5 Flexible system structure
Up to 24 electronic scales can be controlled to meet all rubber production requirements, and one scale can weigh many kinds of raw materials, which reduces the cost of the system.
5 Application of new rubber batching control system
5.1 Batching system control multiple rubber production line batching
With the continuous development of China's rubber industry, some rubber enterprises for various reasons need to use a set of dosage system to multiple rubber production line material supply. Such as Nanjing Sheng Han Rubber Co., Ltd., due to the limitations of the factory site, a set of dosage system to the production line and embossing production line at the same time to provide raw materials, and a lot of scales 2 lines have to be used, but the formula of the white different. The new rubber dosage control system saves the formulas, weighing points, dosage parameters, and storage time sequences of the different dosage methods in the PLC, so that when switching to another dosage method, as long as the computer is switched to the dosage screen the dosage parameters can be switched automatically in the PLC. It avoids the shortcomings of the traditional dosage system, such as increased workload of the operator and the possibility of wrong formula, which are caused by the constant change of the formula, and greatly improves the reliability of the dosage.
5.2 Online switching between old and new batching control system
The continuous production time of rubber factory is generally 5~8 years. During this period, the raw material batching machine has to continuously deliver qualified raw materials to the rubber melting kiln. When the old dosage control system can not meet the normal production requirements, the new weighing control system online replacement without affecting the normal production of rubber production line has become a need. The key to switching between the old and new dosage control systems online is the switchover time. The switchover must be completed within a few hours, and the new system can work reliably immediately, so that the switchover is successful. The new rubber dosage control system can be switched between the old and new dosage control system within 8h. Can be completed in such a short period of time switching is mainly because of the feeding system structure is simple, reliable system, and there is a standard calibration software to make the calibration work greatly simplified.
5.3 Control of special scales
In the production of rubber and other special rubber, some special raw materials in each sub-materials at least only need to add 1g, even after mixing with other raw materials as long as the matching of 100g, which requires high-precision dosage system and special control software.
The new rubber feeding system realizes high-precision control due to its high measuring accuracy and control precision, and the scale control software is directly programmed by PLC, which can prepare corresponding control strategies according to the characteristics of raw materials. The actual accuracy of the new rubber feeding system can reach 2g, which can meet the requirements of various rubber batching.
6 Conclusion
After 8 years of practical application of the new rubber dosage control system, our company deeply appreciates that the control technology of the new dosage control system has reached the advanced level of foreign counterparts, and the price of the whole control system is much lower than that of similar foreign systems. The new rubber dosage control system is not only developed for our rubber production line, in fact, the control system can also be used in building materials, chemical industry, food and other industries in the dosage production line, has a broad market prospect.