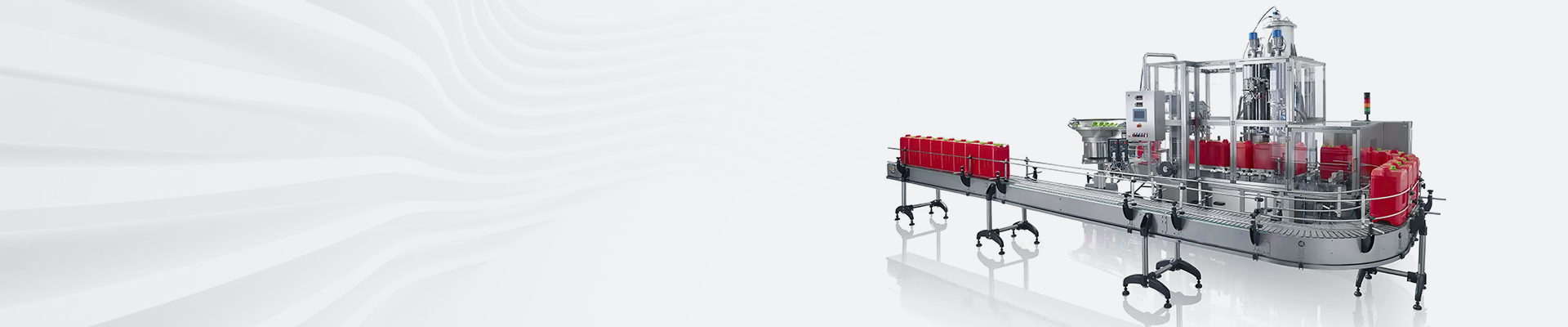
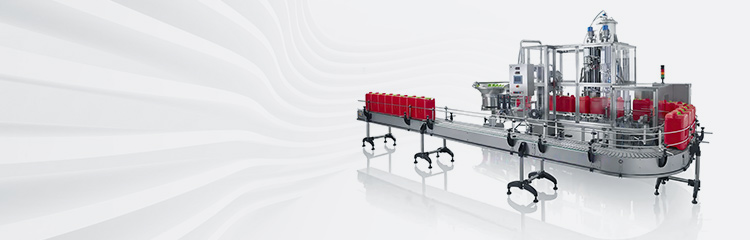
摘要:集散配料系统配置了Modbus模块与触摸屏实现通讯。DCS控制全厂信息的集中监控。采用双层滤波,定量、定速、定时相结合的“切分”控制策略。
一.概况
乳胶漆的生产工艺从其1953年面世以来,经过了50年的发展,今天它已经成为全球最流行的墙面涂料。丙烯酸酯乳胶漆的特点有:涂膜光亮、柔韧,具有优异的黏结性、耐水性、耐碱性和耐候性等性能。其应用范围主要是外墙涂料和内墙高档装饰涂料,这些特点让丙烯酸乳胶漆成为建筑涂料的主流。集散自动配料系统乳胶漆行业的广泛应用,提高企业自动控制及生产安全性及作业效率都有着重要作用。
二.丙烯酸乳胶漆生产工艺
1.单体调配阶段:由罐区按比例进料,调制单体。
难点:此过程配料的种类繁多,比例灵活多变,要求较高的定量调节精度,且对现场及控制室操作人员要求较高。
2.反应阶段:调制好的单体和预先调配的引发剂同时匀速滴加进反应釜,并通过蒸汽及冷却水调节反应釜温度。
难点:由于物料及工艺特殊性,部分匀速滴加物料管道并没有流量计,需要对称重进行数据的处理转换成流量;
3.成品调配阶段:反应釜物料进入调配釜,匀速滴加氧化剂还原剂等添加剂,经过冷却控温,得到成品乳胶漆。
难点:氧化剂、还原剂的流量转换及比值控制。
现场反应釜
三.丙烯酸乳胶漆生产工艺难点分析
重点及难点有三个方面:
1.反应釜的控温:反应釜温控精度灵敏度要求很高,温度过低会导致反应无法发生,造成“僵釜”现象,影响生产效率,温度过高反应生成物中会含有较多杂质,并且涨势太快压不住温又会导致“飞温”,容易发生事故。可反应放热、物料的比热、加热功率、保温层保温效果、釜体本身的散热、环境温度和不同物质的吸、放热的特性等不同因素都会对反应釜温度产生不同的影响。各种因素之间相互耦合、影响,控制特性比较复杂,且温度变化滞后。反应釜温度又随着反应的发生呈现时变性,所以很难确定精确的数学模型。
2.现场及中控人员配合减少误操作:现场端配有就地操作触摸屏,负责具体的操作,中控室负责全局的把控和分工段操作的监控,这要求控制设备具有灵活的人机交互功能及强大的扩展通讯功能。
3.称重转流量后的比值滴加调节:称重转流量具有较大的滞后性,对现场称重仪表及阀门精度要求较高,且要求DCS控制设备,保证实现复杂的控制策略,且运行和操作的自动化程度高。
四.解决方案
1.对于反应釜的温控,通过过往优稳工程的控温经验及现场的实际情况,聚合釜温度采用模糊控制加PID控制即采用FUZZY-PID双模控制方案,当温度误差在某个标定值以外时,采用模糊控制,以获得良好的瞬态性能;当温度误差在标定值以内的范围时,则采用PID控制,以获得良好的稳态性能。这种FUZZY-PID复合控制方式比单纯的模糊控制具有更高的稳态精度,更大程度上保证了反应的温度条件,获得了明显优于PID控制的良好效果。
2.对于现场的分工配合,优稳DCS利用其灵活的人机交互功能及强大的扩展通讯功能,与现场几十台触摸屏通过Modbus通讯,实现了现场端负责具体的操作,中控室负责全局的把控和分工段操作的监控,通过优稳DCS强大功能使现场权限明确,分工仔细,减少了人为失误,确保了平稳高效的生产。
3.称重投料系统对于称重转流量后的比值滴加调节,经过优稳工程团队的多次试验,必须处理现场称重的实时扰动及转换后流量调节的滞后问题,于是采用双层滤波,定量、定速、定时相结合的“切分”控制策略,很好的解决了这类纯滞后的复杂控制问题,保证业主生产需要的同时,节省了前期投资的成本。
称重转换算法(部分)
五.配置说明
1.上料系统配置:
本工程配置4个控制站,4台操作员站(可兼作工程师站)。
各工段还配置了Modbus模块与触摸屏实现通讯。触摸屏用于就地显示数据和就地操作;
配置冗余光纤交换机,将各现场控制站的数据通讯到中央控制室,中央控制室配置两台监控站,实现全厂信息的集中监控。其中一台监控站和打印机相连,实现日常的生产控制、监测、报警及报表输出等操作,另外还配置了大屏显示系统;
2.产品特点:
全冗余设计方式:电源模件、控制模件、I/O模件、控制网络、系统网络均支持硬件双重化(三重化)冗余,零切换时间,保证控制的连续性;
高可靠I/O模块:点点隔离、点点互隔、点点配电、在线点点更换,可满足核电、紧急停车等高可靠性高安全性领域要求;
部件智能设计:模件、模块均配置微处理器或多处理器,少类型多功能,软件选择信号类型,减少备品备件,在线校正,自动补偿;
低功耗设计:无需强制散热,适应恶劣的工业环境;
运行安全设计:实时数据库掉电保持,冗余校验,快速恢复,保证系统信息安全;
开放式模块化结构设计:取消机笼、底板、端子板等,双面安装,节省转接电缆与机柜;
分布式全局实时数据库,数据规模10万点,高效压缩算法,数据全局直接引用;
IEC61131-3标准,FBD、LD、SFC、ST、IL多种语言混合编程环境,在线编程、模拟调试;
实时数据质量戳功能,保证实时数据的可靠性与可信度;
C/S或B/S模式,Web访问,PC机、iPAD、iPhone、Android等智能终端可直接浏览;
六.小结
该工程自从用集散喂料系统投运以来,运行平稳,效果显著,操作平稳率,产品质量等都大大提高;特别是工人劳动强度,原料消耗等都有大幅度降低,同时也确保了装置的平安全运行。直接提高了企业的市场竞争能力,为企业带来了十分明显的经济效益。